What coffee roasters needs to know during roasting: Air Pressure Stabilization
In the previous column "Understanding What is a Differential Pressure Gauge?", we mainly learned the following three things:
- The pressure difference inside and outside the boiler can reflect the true exhaust volume.
- The same volume of the exhaust does not necessarily represent the same exhaust volume; but the same pressure difference can definitely represent the same exhaust volume.
- If the exhaust pipe is blocked, even if the same volume exhaust is opened, the pressure difference inside the drum will be lower. At this time, it is necessary to increase the exhaust % to compensate for the reduced exhaust volume due to the obstruction, so that the pressure difference inside the drum can be maintained at the same number as before.
Therefore, if the roasting machine itself can automatically compensate for the differences through measuring the pressure value, it can minimize the exhaust reduction caused by the cleaning of the exhaust pipe. Roasting machines equipped with a "differential pressure compensation system" can automatically compensate for the exhaust in real-time by measuring the differential pressure data and performing computer calculations to maintain a stable pressure difference. This ensures that the original flavor creation, achieving more accurate flavor reproduction.
Why roasters need the air pressure compensation system?
Exhaust Stabilization
After using a roaster for some time, oil and dust will accumulate on the exhaust pipe, causing exhaust burden. With the same roaster and the same size of damper, the number of pressure difference will gradually decrease over time. However, different exhaust volumes produce significantly different flavor characteristics, such as changes in air flow, changes in convective heat, and exhaust volume, all of which are critical factors affecting the flavor in the roasting process. With the air pressure compensation system, it will effectively reduce the unstable factors of exhaust volume, enabling the roaster to more accurately reproduce the classic flavor of the roaster.
Extend the Cleaning Cycle
One of the biggest challenges for most coffee roasters is the cleaning process of the roasting machine. Apart from being a time-consuming and labor-intensive task, roasters also need to readjust their roasting profile after cleaning to ensure that the flavor remains consistent. For commercial roasting businesses, downtime of the roasting machine due to cleaning is also a significant consideration in terms of operational costs. Therefore, extending the cleaning cycle can reduce business losses. Rubasse Air pressure compensation system can compensate for reduced exhaust airflow due to pipe blockages by automatically adjusting the exhaust to maintain a stable exhaust airflow. After cleaning, there is no need to spend additional time calibrating roasting techniques, allowing for continuous production and supply without significant variations.
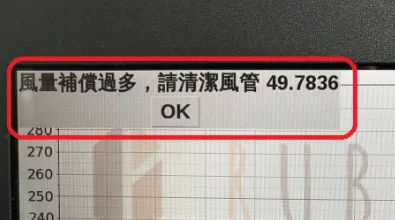
Image 1: Rubasse cleaning notification reminder for the Air pressure compensation system, preventing excessive blockage of the exhaust system, which can cause more severe issues.
In addition, professional roasters usually monitor the differential pressure gauge to determine if the exhaust system needs cleaning. If the roasting machine's detects that the differential pressure values are not reaching the same level for the same airflow, it will automatically prompt a window to remind the user to perform routine cleaning, allowing roasters to focus on their roasting process without worrying about the cleanliness of the machine.
The idea behind the design
When the coffee roaster is clean and the exhaust is smooth, there will be corresponding differential pressure values for each exhaust %. As shown in Figure 2, when the exhaust of the roaster is set to 80%, the reading on the differential pressure is approximately 40Pa.
When we roast a large amount of coffee beans, the pipeline will begin to get blocked, and the exhaust pipe will become clogged, as shown in Figure 3.
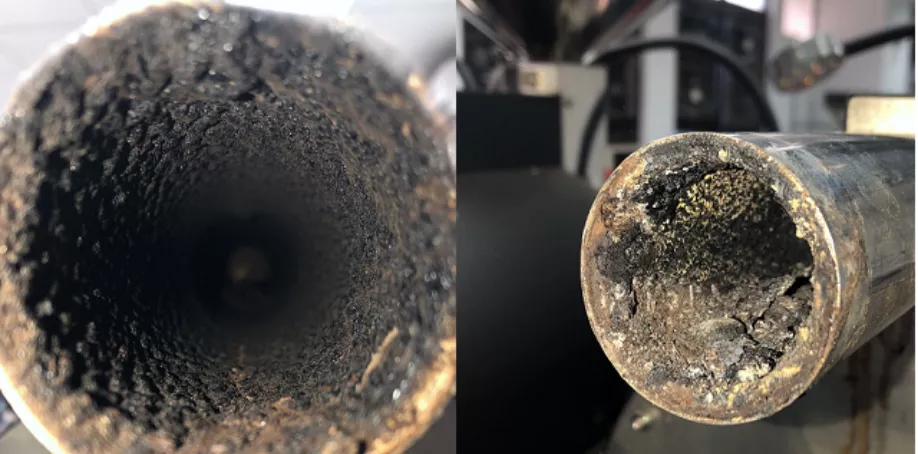
Figure 3. Image of the blocked exhaust pipe after roasting a large amount of coffee beans.
We used tape to cover 2/3 of the surface area to simulate a blocked air duct. As shown in Figure 4.
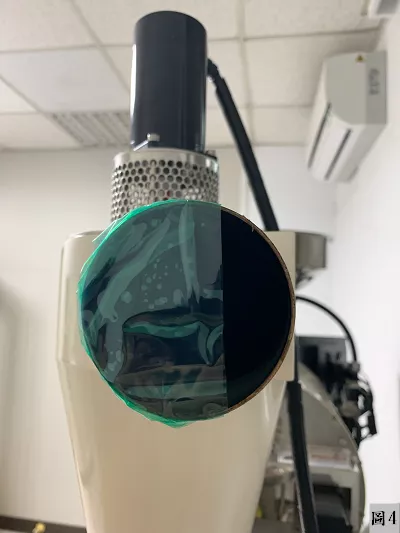
Image 4: Taping 2/3 of the area of the exhaust pipe to simulate a 66% blockage situation.
When a roasting machine is equipped with a pressure compensation system, it can control the pressure difference to stabilize the actual exhaust volume. Taking the example of the fully automatic mode of the Rubasse roasting machine, if the current pressure difference is too low, the machine will automatically adjust the exhaust to maintain the consistent air pressure with the recorded value. As shown in figure 2, the pressure difference value of about 40pa should be achieved at 80% exhaust. However, when the machine is blocked (as shown in figure 5), the pressure difference decreases by about 15pa.
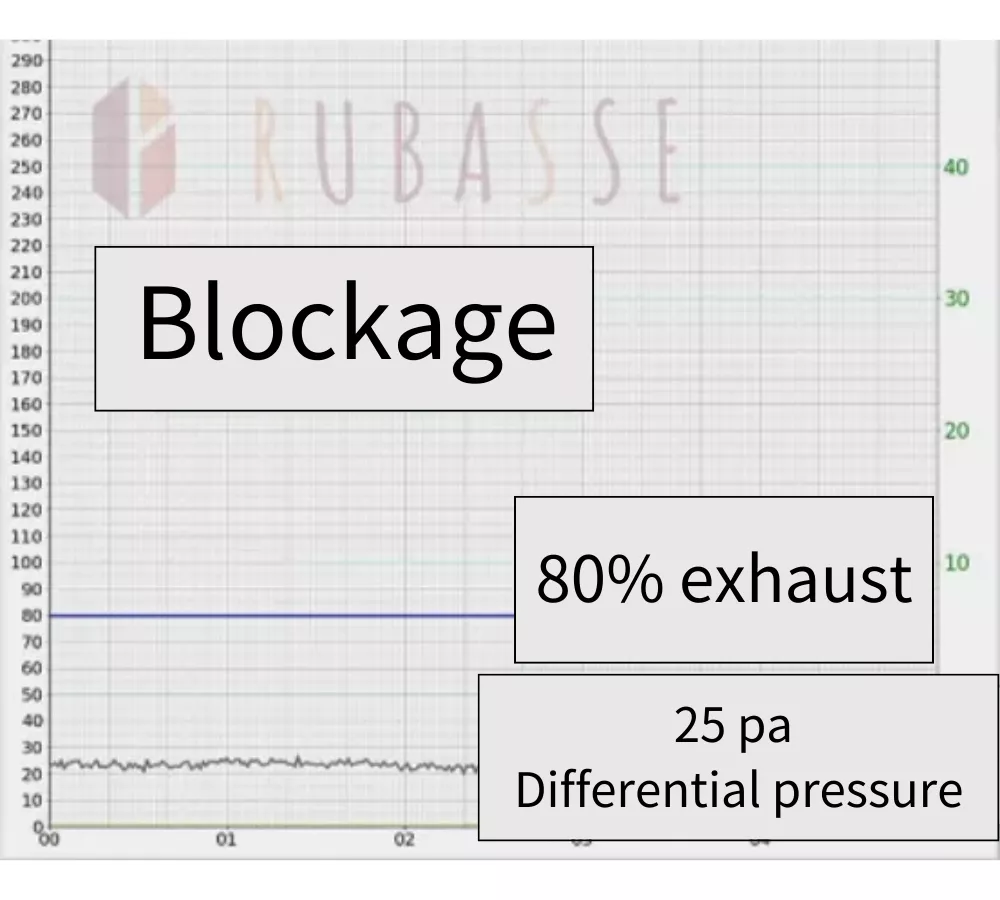
Figure 5. Measurement after blockage, wind speed at 80%, pressure difference value is about 25Pa. (When unblocked, wind speed at 80% has a pressure difference of about 40Pa)
To reproduce the exhaust volume that should have been present at the time, the system intelligently increases the air damper to around 100%, thereby reproducing the pressure difference value (the actual exhaust volume that should have been present) in the recorded curve within an extremely short period of time, as shown in Figure 6.
Figure 6. After activating the Air pressure compensation, the exhaust is intelligently adjusted to the exhaust volume as roasting profile.
Even under more extreme blockage conditions, as shown in Figure 7.
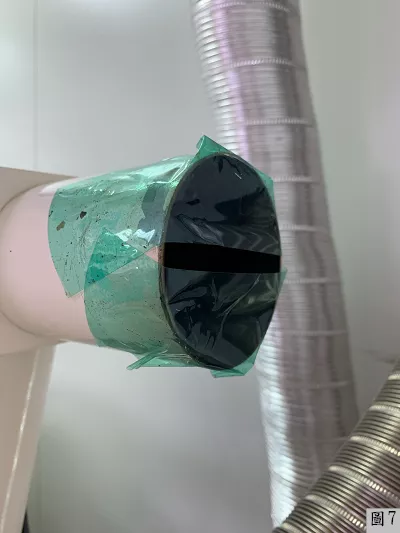
Figure 7. Simulated extremely blocked air duct.
The air pressure compensation can still compensate for the lost exhaust volume due to blockage within a short period of time, as shown in Figure 8.
Figure 8. Through real-time computer calculation, the differential pressure value is tracked and the exhaust volume of each batch is stabilized
Experiment
We designed an experiment to test the effectiveness of the pressure compensation system. Figure 9 shows that, in order to simulate a real-life blocked air duct, we used tape to cover approximately 50% of the surface area of the air duct.
Figure 9: Simulated blocked air duct
In the experiment, we selected a curve as shown in Figure 10 and used the Rubasse fully automatic mode to reproduce the roasting profile. We compared the results between using and not using the Air pressure compensation system.
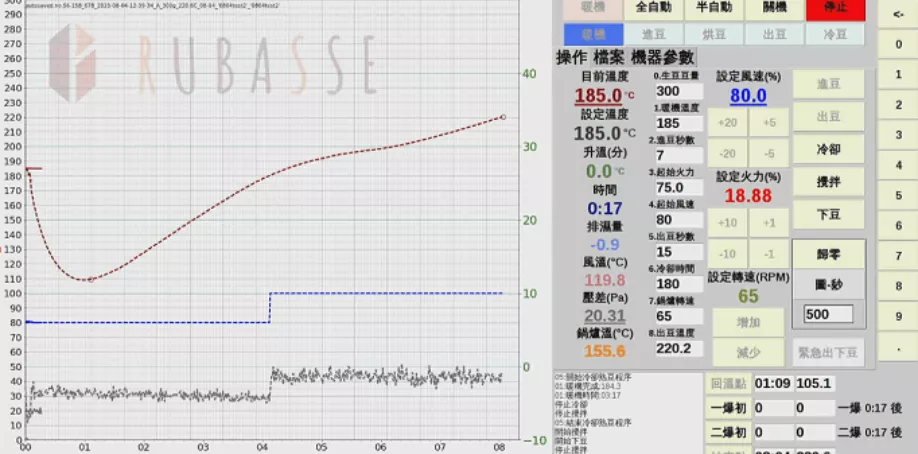
Figure 10: Original poasting profile.
Roasting machine without Air pressure compensation.
Figure 11: A Rubasse roasting machine without pressure compensation, with only exhaust and fire replication system, according to the roasting curve.
In the case of pipe blockage, most roasting machines on the market have different exhaust volumes even if the same exhaust control is used according to the roasting profile, which varies depending on the model, as shown in Figure 11. Although the computer reproduced the exhaust curve during extreme blockage, the pressure difference was as much as 20 Pa. This once again verifies that "the same exhaust percentage does not necessarily mean the same exhaust volume." This is why roasters need to clean the machine and calibrate the technique regularly.
Activating Air Pressure Compensation System
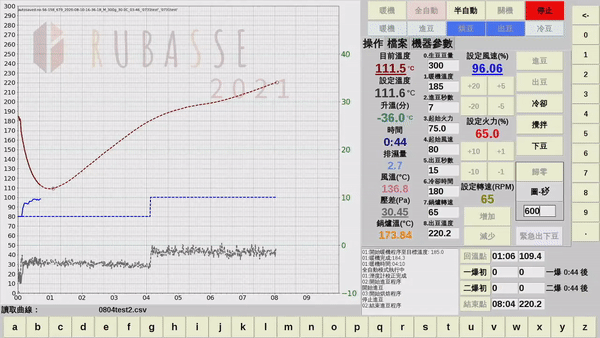
Figure 12: Opening the Air pressure compensation system.
By controlling the differential pressure to stabilize the actual exhaust volume, as shown in Figure 12, even in the case of severe blockage in the exhaust system, the air pressure compensation can ensure consistent exhaust volume for each roasting batch and compensate for the differential pressure caused by blockage. The computer appropriately increased exhaust volume, making the differential pressure tend toward the recording curve. The entire bean temperature reproduction process will not have any deviation. Even if the exhaust pipe is blocked, after opening the pressure compensation function, the temperature will be exactly the same as the original profile, without being affected by the blockage, perfectly reproducing the roasting profile!"